Articles By Our Members
Low-cost Duplication of a Boat Hull Using Polyester Fiberglass
by Brian Clarke, November 2003
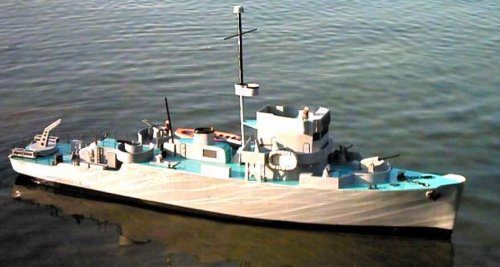
"Admirable" Class Minesweeper, 46 inch long.
The following technique is derived mainly from trial-and-error over
several years using polyester fiberglass resin. Polyester resin
attacks styrofoam and styrene plastic, smells like acetone (nail polish
remover) and is a carcinogen. I suggest ventilation and disposable rubber
gloves.
Epoxy resin would probably provide a better quality hull, does not
smell, but is about four times as expensive as polyester resin. The choice
is yours.
Materials required:
- 2 litre Motomaster Fiberglass Liquid Resin (includes hardener), $15 per
litre, Canadian Tire.
- 1 square meter, Fiberglass Mat (random fibers), $5, Canadian Tire.
- 454 g, TREWAX Clear Paste Wax, $10, Home Hardware.
- Several cheap 1 inch to 2 inch paint brushes, 50 cents each, Dollar
store.
The mold and hull for a 46 inch minesweeper hull each cost about $25 + tax
(polyester resin).
Fabricating the Mold
The original hull should be stripped of rudder, propeller and shaft and
as much superstructure as is possible. All parts of the remaining
superstructure should be covered (protected from spattered resin).
Prop shaft and rudder holes should be covered with masking tape. Wax the
original fiberglass hull twice, as a mold release agent. Paste wax works
well, car wax might work.
If you are concerned with damaging the original hull, an aluminum foil
barrier can be used to protect it. Strips of aluminum foil, about .75 inch
wide, can be attached to the hull, slightly overlapping, using a very
light coating of spray adhesive on the foil. The foil is then waxed.
Remember, you have to remove this foil later without damaging your hull.
Strip width depends on the curvature of the hull.
If the hull shape is complex, as in a submarine, a split-mold (made in
two pieces) ensures that the hull will be released from the mold easily and
can be made as follows: cut two pieces of 1/8 inch plywood (doorskin) to
conform to the shape of the keel. Use screws to hold the wooden pieces
together, then make half the mold at a time.
Polyester resin will start to gell and be unusable in the can about 15
minutes after being mixed with hardener, so use two people, prepare
everything and work fast! Pouring the resin onto the mat will slow
the cure a little. Mix only as much resin as you can use in 15 minutes!
Mix some resin (150 ml) and a few drops of hardener thoroughly in a clean
tin can. Paint the waxed hull with a coat of resin and leave to cure. Throw
the brush away.
The next layer is fiberglass mat (pre-cut to fit) and resin. Spread resin
on the hull, place the mat on the wet hull then spread more resin through
the mat. Tap the resin-soaked cloth with the tip of the brush all over,
removing the air bubbles (this is very important). Don't be slow!
Wooden ribs, located on the outside keep the mold rigid. Leave to cure
overnight.
Carefully peel the mold from the original hull. A thin metal ruler
carefully slipped between the original hull and mold can help break the
surface tension.
Fabricating the New Hull
Wax the inside of the mold twice (including the wood if a split-mold is
used).
Apply a coat of resin to the mold and let cure.
Apply another coat of resin to the mold then put the pre-cut mat into the
mold, saturate it with resin and tap the saturated cloth all over with the
tip of the brush to remove bubbles (this is very important). Only apply
enough resin to saturate the mat. If the hull is large, do it in two parts
or use two people; brushes are cheap.
Allow to cure overnight, then peel from the mold. Additional hulls can be
made from the same mold for about $25 each. Wax the mold each time.
N.B. Don't forget to wax the original hull and mold each time!!!
Brian Clarke
|